When we speak about balancing in the world of automobiles, the first thing that comes to mind is balancing wheels. It’s a maintenance procedure that almost everyone on the road today is familiar with. Regardless of the vehicle in question, balanced wheels are hugely important as it’s responsible for making sure your wheels are turning as they should.
Another component that also requires being perfectly balanced is brake rotors. However, it’s far less common because most rotors are balanced right out of the box whereas wheels require to be balanced with each tire change. Rotor balancing, as its name suggests, ensures that there are no imbalances and helps maintain a smooth driving experience. Read on to learn more about this fairly uncommon, but an interesting procedure.
Article updated on 05/17/22. Original publishing date 03/16/21

What is Rotor Balancing?
Rotor balancing is the process of equalizing the distribution of mass to ensure that there are no imbalances. This procedure ensures that the rotor isn’t facing an inadequate mechanical balance or unbalance.
Brake rotors are manufactured using the casting method. Casting is a procedure in which a substance in liquid form is poured into a mold and allowed to solidify by cooling. This mold is essentially a hollow cavity of the desired shape and in this case, it’s the shape of a rotor.
While the technology around castings has improved considerably in recent years there are still areas in which one can notice inconsistencies. Castings need to undergo a treatment like machining after solidifying to make certain that it doesn’t encounter any imbalances. However, brake rotors have inaccessible areas like the cooling vanes inside of a vented rotor that cannot be machined. As a result, it can develop an imbalance. Simply put, an imbalance is when one side of a rotor is heavier or lighter than the other.
Brake rotor manufacturers are aware of this and most of them see to it that a rotor doesn’t leave their facility if it isn’t balanced. Just like with wheels, rotor balancing is the method of adding or removing weight to the brake rotor to establish its effective mass centerline approaches the true axis. Rotor balancing safeguards vehicle owners from problems like noise, vibrations, pedal pulsation, and more.
How Do You Balance Brake Rotors
The most widely used method of rotor balancing is removing material from the outer edge of the rotor. The first signs of an imbalance are when the center of the rotor at speed moves out from its rotational axis, causing an imbalance. To address this, the brake rotor is put through both horizontal and vertical machines. For reference, wheels are only put through a vertical balancing machine.
The brake rotor is installed on the machine and is supported by bearings, and the machine spins the rotor. With brake rotors getting larger even the most minor imbalances result in noticeable problems, making the rotor balancing procedure more important than ever. If the rotor balancing machine being used is of the automated type, it’ll detect inputs like the weight, dimensions, and displacement automatically.

Once the machine has the information it needs, it’ll spin the rotor until it finds the unbalance present. A rotor balancing machine determines the exact location and mass of the unbalance. After this, it’ll mill or drill out a certain amount of material from the edge of the rotor which it identifies as the heavy position.
This will almost always be the route a modern rotor machine will take. These machines are incredibly impressive as they can easily and accurately identify any mass axis 0.001 mm off the running axis.
Sometimes, however, balance weights are added or welded to the light position of a rotor. This is quite uncommon, but not unheard of. Drilling or milling is usually the option as it can’t fail like a weight being added on. There have been instances where balance weights have been added to the vanes between the brake rotors which over time have failed and dislodged themselves. This can upset the balance of the rotor and result in several complications.
The most efficient types of rotor balancing machines can detect and address all three types of unbalances – static, couple, and dynamic. While we’ll discuss the differences between the three in a bit, it’s important to know that some machines can only identify a static unbalance. Some rotor balancing machines will only identify unbalances in two axial planes.
Types of Brake Rotors
In regard to rotor balancing, brake rotors can be divided into two groups – rigid and flexible.
The first type of brake rotor is the one that falls in the rigid group. A rigid brake rotor doesn’t deflect at any operating speed. Simply put, the speed of its rotation doesn’t affect its balance. What this also means is that if a rigid brake rotor were to have an imbalance, it would be evident at any speed in the operational range. As a result, rigid rotors can be put through the rotor balancing procedure at a low speed, just enough to produce a centrifugal force to register the imbalance.
The second type of brake rotor is of the flexible type. These flexible brake rotors are known to bow as the speeds increase. In most cases, a flexible rotor is balanced at a low speed where the rotor does not flex. However, as a flexible rotor continually changes its configuration as it reaches higher speeds, balancing it is more complex. When flexible brake rotors undergo the rotor balancing procedure, corrections for the imbalances are made in stages. Rotor balancing machines will make these systematic corrections until the rotor’s maximum operating speed is achieved.
Types of Brake Rotor Unbalances
There are three types of unbalances – static, couple and dynamic unbalance.
Static Unbalance

Static unbalance is also referred to as force or kinetic unbalance. When this occurs it means that the principal axis has moved out of position to the shaft axis or when its principal axis is displaced parallel to its rotational axis. This is one of the easier unbalances to fix as it is corrected only in one axial plane. Oftentimes, brake rotors with diameters much larger than their width are balanced in a single plane to correct the static unbalance.
Couple Unbalance
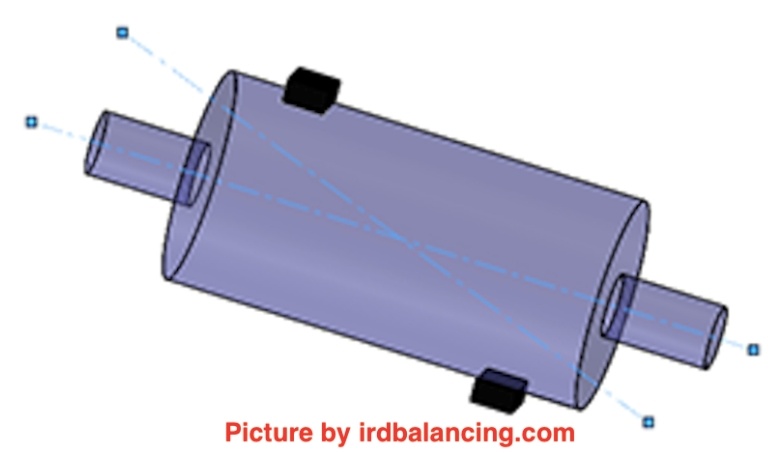
If your brake rotor has a couple unbalance, that means its principal inertia axis is displaced from the rotational axis, and they intersect at the center of gravity. Essentially, it occurs when the principal axis intersects the shaft axis at the rotor’s center of gravity. The imbalance is usually corrected by considering vibration measurements with the rotor turning and adding correction masses in two planes.
Dynamic Unbalance

A dynamic unbalance of the brake rotor is a mix between static and couple unbalances. A brake rotor is faced with a dynamic unbalance when the principal inertia axis is displaced from the rotational axis while also not intersecting at the center of gravity. To put it simply, it occurs when the central principal axis and shaft do not intersect or align parallel to one another.
At this point, the vibration amplitude and the phase angles of the brake rotor will differ. The method of fixing a dynamic unbalance is similar to that of fixing a couple unbalance.
Can Any Rotor Be Balanced?
No, brake rotors that have crossed a certain extremity of unbalance cannot be balanced. While the different types of unbalances and their corrective measures may lead you to believe that any rotor can be balanced, that’s not the case as this procedure has its limits. Rotor balancing can only be carried out when the level of severity of the unbalance is acceptable.
International and national standards are quoted for rotors, for example, car wheels are balanced to a limit of grade 40, and small electrical armatures are balanced to grade 2.5. According to ISO 1940 standards, the grades are converted to unbalance units, depending on the operational speed of the rotor.
Balance or Replace Your Rotor
Thanks to the latest tech, rotor balancing is easier and more affordable than it used to be. Many machine shops nowadays are equipped with automatic rotor balancing machines making the process quite convenient.
However, if your brake rotors are severely unbalanced, no machine will be able to fix them as we mentioned above. At this point, you should get brand-new rotors and ones that are OEM quality, so they come balanced right out of the box. Conveniently, you can find them right here at our store section for a huge variety of cars.